5 min read
Predictive Maintenance: Reducing Downtime
Focus on how Tasklytic helps manufacturers predict equipment failures and optimize maintenance.
Written by
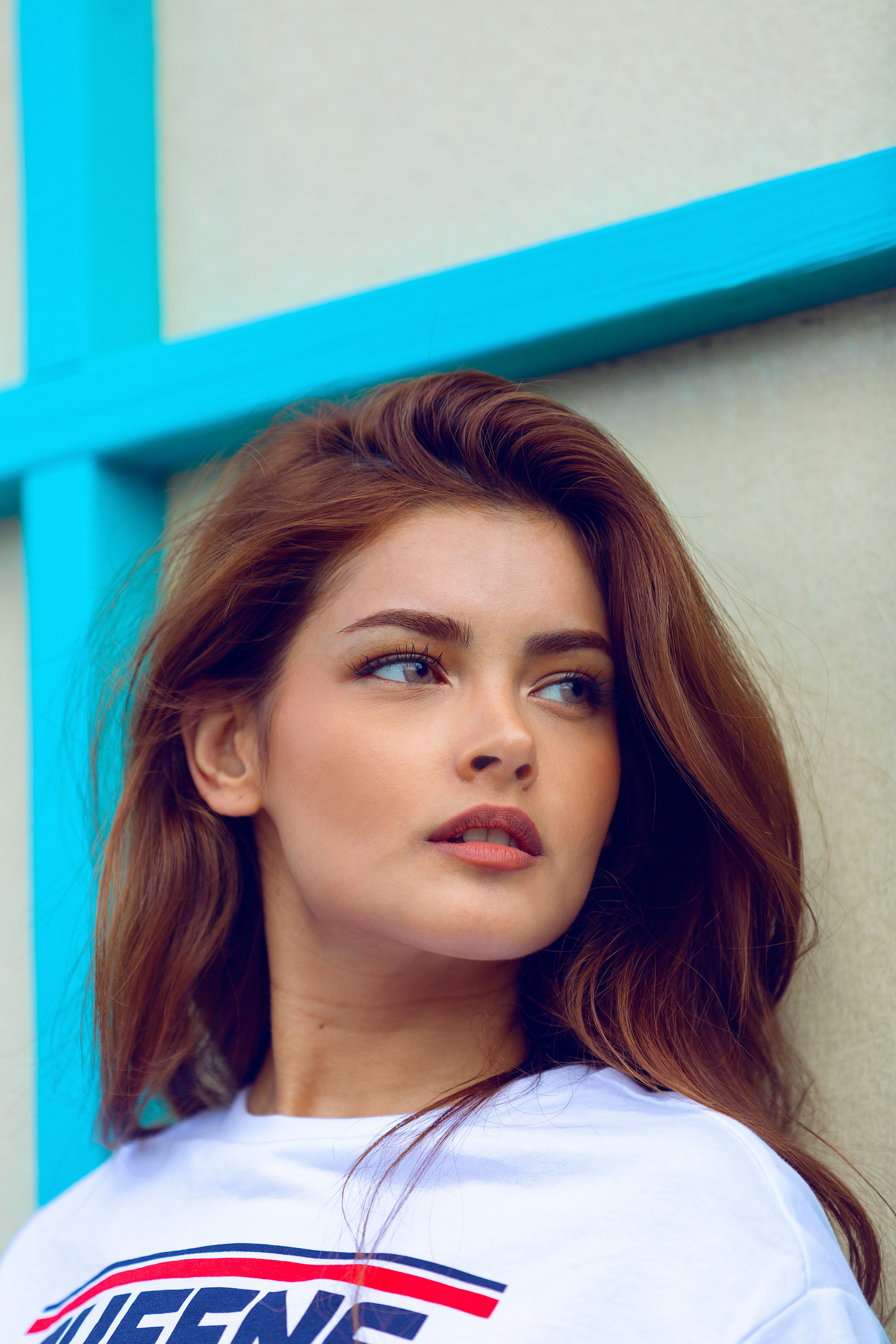
Elleana Dsouza
Published on:
25 June, 2024
In manufacturing, equipment downtime can disrupt production, inflate costs, and affect quality standards, ultimately impacting profitability and customer satisfaction. Predictive maintenance, powered by advanced analytics, enables manufacturers to anticipate equipment failures and perform maintenance only when necessary, significantly reducing unplanned downtime and maximizing operational efficiency. Tasklytic’s analytics platform provides manufacturers with the tools needed to monitor equipment health, predict potential failures, and schedule timely maintenance, transforming reactive maintenance into a proactive strategy that keeps operations running smoothly.
The Importance of Predictive Maintenance in Manufacturing
Traditional maintenance approaches—such as reactive maintenance (fixing equipment after it fails) and preventive maintenance (regularly scheduled maintenance)—can either be costly or inefficient. Reactive maintenance leads to unexpected downtime, while preventive maintenance can result in unnecessary part replacements and labor. Predictive maintenance, driven by real-time data analytics, addresses these issues by optimizing maintenance schedules based on equipment condition. Here’s why predictive maintenance is essential:
Reduced Downtime: By addressing issues before they result in equipment failure, predictive maintenance keeps operations running smoothly.
Cost Efficiency: Predictive maintenance reduces maintenance costs by scheduling interventions only when necessary, avoiding unnecessary part replacements and labor costs.
Extended Equipment Lifespan: Regular monitoring helps maintain optimal operating conditions, extending the lifespan of machinery.
Implementing Predictive Maintenance with Tasklytic: Step-by-Step Guide
Here’s how manufacturers can leverage Tasklytic’s predictive maintenance features to reduce downtime and optimize operations:
Integrate Tasklytic with Equipment Sensors: Connect Tasklytic to sensors and data sources across your machinery to gather comprehensive performance data in real time.
Define Key Performance Indicators (KPIs): Set critical metrics to monitor, such as vibration levels, operating temperature, and power consumption, that Tasklytic will track for predictive insights.
Configure Predictive Alerts: Set up Tasklytic to send automated alerts based on predictive insights, enabling the maintenance team to act before potential issues become costly.
Analyze and Adjust Maintenance Schedules: Use Tasklytic’s insights to fine-tune maintenance schedules, shifting from time-based to condition-based maintenance.
Monitor and Refine: Continuously monitor Tasklytic’s insights and update maintenance protocols based on evolving data patterns.
The Future of Maintenance: Predictive, Data-Driven, and Proactive
As manufacturing technology advances, predictive maintenance will play an increasingly crucial role in ensuring uninterrupted operations. Tasklytic is at the forefront of this shift, offering a powerful platform for data-driven maintenance that reduces downtime, minimizes costs, and maximizes productivity. Predictive analytics are transforming maintenance from a costly necessity into a strategic advantage, empowering manufacturers to optimize performance, extend equipment life, and keep up with industry demands.
Get Started with Tasklytic for Predictive Maintenance
Don’t let unexpected breakdowns hold your operations back. With Tasklytic’s predictive maintenance features, manufacturers can take control of equipment health, reduce downtime, and boost efficiency. Begin transforming your maintenance approach today and see the impact of data-driven insights on your production floor.
Other Popular Blog Posts
Discover additional features designed to elevate your experience and drive success.